در ابتدا و در توضیح نحوه تولید ورق آلیاژی باید این نکته را بدانید که فلزات در حالتی که خلوص کامل داشته باشند، معایبی را خواهند داشت به همین دلیل در این حالت معمولا از آنها استفاده نمی شود. به همین علت و برای قابل استفاده بودن، خواص مکانیکی و شیمیایی فلزات دستخوش تغییر می شود
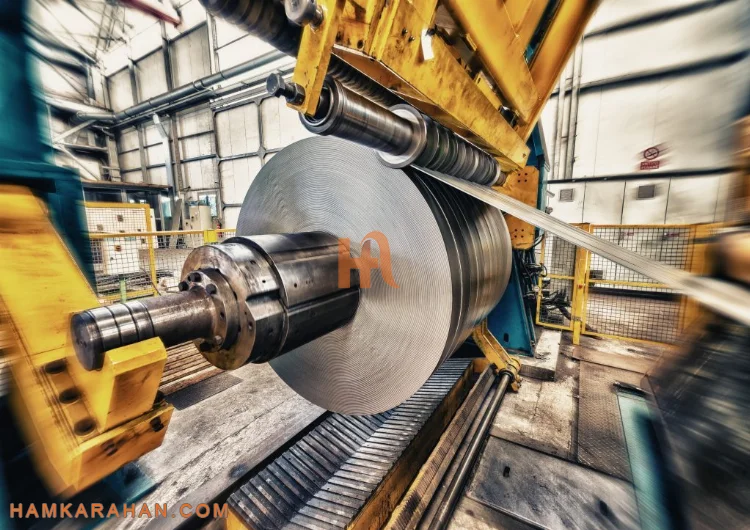
عناصری همچون منگنز، نیکل کروم و کربن به ساختار آنها اضافه می شود. با ترکیب این عناصر، آلیاژ به دست می آید. برای ساخت ورق آلیاژی از روش های مختلفی استفاده می شود. در ادامه به بررسی هر یک از این روش ها می پردازیم. یکی از معمول ترین روش هایی که برای تولید ورق آلیاژی استفاده می شود ذوب کردن فلزات و عناصر است. در دامه توضیحات بیشتری از روش های تولید ورق آلیاژی می دهیم.
تولید ورق های آلیاژی به روشهای مختلف
امروژه آلیاژها با روش های مختلفی تولید می شوند. این روش ها ممکن است با ترکیب فلزات پایه و برخی عناصر ایجاد شوند. این مورد را در نظر داشته باشد که مخلوط کردن فلزات و تولید آلیاژ با روش های مختلفی صورت می گیرد.
تولید ورقهای آلیاژی به روشهای مختلفی انجام میشود که هر کدام بسته به نوع آلیاژ، کاربرد نهایی و ویژگیهای مکانیکی مورد نیاز انتخاب میشوند. در ادامه به مهمترین روشهای تولید این ورقها پرداخته میشود:
1. نورد گرم (Hot Rolling)
- در این روش، شمش یا تختال آلیاژی در دمای بالا (بیشتر از دمای تبلور مجدد) گرم شده و از میان غلتکها عبور داده میشود تا به ضخامت مورد نظر برسد.
- این فرایند باعث کاهش تنشهای داخلی و بهبود خواص مکانیکی میشود.
- کاربرد: صنایع ساختمانی، خودروسازی، کشتیسازی و تولید مخازن تحت فشار.
2. نورد سرد (Cold Rolling)
- در این روش، ورقهای تولید شده توسط نورد گرم، بدون افزایش دما، از میان غلتکها عبور داده میشوند.
- نتیجه این کار، افزایش سختی، دقت ابعادی و کیفیت سطحی بهتر است.
- کاربرد: صنایع خودروسازی، لوازم خانگی، تولید قطعات دقیق و صنایع بستهبندی.
3. ریختهگری مداوم (Continuous Casting)
- در این روش، فلز مذاب مستقیماً به صورت ورق یا تسمههای نازک ریختهگری میشود.
- این روش بهرهوری بالایی داشته و امکان کاهش هزینههای تولید را فراهم میکند.
- کاربرد: تولید فولادهای آلیاژی و ورقهای خاص.
4. فورجینگ و نورد ترکیبی (Forging & Rolling)
- در برخی موارد، ابتدا فلز تحت فرآیند فورجینگ شکلدهی شده و سپس با نورد، به ضخامت مورد نظر میرسد.
- این روش برای تولید ورقهایی با استحکام بالا و ساختار ریزدانه به کار میرود.
- کاربرد: صنایع هوافضا، نظامی و خودروهای سنگین.
5. متالورژی پودر (Powder Metallurgy)
- در این روش، پودر فلزات آلیاژی فشرده و سپس در دمای بالا تف جوشی (Sintering) میشود تا ورقهای نازک تشکیل شوند.
- این روش برای تولید ورقهای خاص مانند ورقهای مقاوم به دماهای بالا یا خوردگی کاربرد دارد.
- کاربرد: صنایع الکترونیک، هوافضا و مهندسی پزشکی.
6. پاشش حرارتی (Thermal Spraying)
- در این روش، ذرات فلزی آلیاژی به صورت مذاب یا نیمهمذاب روی یک سطح پایه پاشیده شده و تشکیل یک لایه نازک میدهند.
- بیشتر برای پوششدهی ورقهای پایه و ایجاد ورقهای ترکیبی استفاده میشود.
- کاربرد: صنایع هوافضا، پزشکی و مهندسی سطح.
هر یک از این روشها مزایا و معایب خاص خود را دارند و بسته به نیازهای صنعتی، هزینه تولید، دقت ابعادی و ویژگیهای مکانیکی مورد نظر انتخاب میشوند.
تولید ورق آلیاژی به روش سنتی
قبل از توضیح این روش باید گفت که برای تولید ورق آلیاژی در ابتدا ضخامت تختال ها کاهش پیدا می کند. برای تولید ورق آلیاژی با این روش در ابتدا تختال ها تولید می شوند. یکی از اصلی ترین مراحل در تولید ورق آلیاژی ذوب کردن و ناصر و تبدیل به حالت مایع است. برای اجرای این روش در ابتدا فلزات و مواد اولیه در کوره های ذوب قرار می گیرند تا فرآیند ذوب شدن آنها انجام شود. بعد از این مرحله مواد آلیاژی به ترکیب اضافه می شود و آلیاژ نهایی تولید می شود. بعد از ذوب شدن مواد، مخلوط مذاب در قالب های خاصی ریخته می شود تا فرآیند خنک شدن به خوبی صورت گیرد. این روش برای تولید آلیاژهای فولادی و برنجی که در اکثر صنایع رایج هستند به کار می رود.
تولید آلیاژ به روش متالوژی پودری
یکی از روش های مدرن در تولید ورق آلیاژی، روش تولید متالوژی پودری است. در این روش ابتدا فلزات و عناصر را به حالت پدر در می آورند و سپس با هم مخلوط می کنند. بعد از این امر، مخلوط ها در قالب های مخصوصی ریخته می شود و با اعمال فشار و دمای زیاد به آلیاژ تبدیل می شود. این روش در سال های اخیر رواج بسیار زیادی پیدا کرده ایت و به وفور از آن استفاده می شود. در ادامه به کاربرد این روش در صنایع اشاره می کنیم.
- ترکیب کردن فلزات با نقطه ذوب بسیار بالا برای اجرای فرآیند ریخته گری در صنعت خودروسازی و تولید لوازم خانگی
- ساخت قطعات فلزی مثل یاتاقان خودرو
- تولید قطعات دقیق و با ظرافت بالا مثل چرخ دنده ها
توجه داشته باشید که استفاده از متالوژی پودری برای تولید ورق آلیاژی مزیت های زیادی دارد. یکی از مهم ترین مزیت های این روش تولید مواد ضایعاتی کم، سازگاری زیاد با محیط زیست، امکان تولید قطعات با شکل ها و فرم های مختلف، افزایش بهره وری انرژی و قیمت مقرون به صرفه اجرای متالوژی پودری از دلایل محبوبیت آن است.
روش کاشت یون ها
سومین روش که برای ساخت ورق آلیاژی مورد استفاده است. روش کاشت یونی می باشد. در این روش یون ها به صورت پرتوهایی هستند که به سطح فلزات شلیک می شوند. این روش با دقت بسیار بالایی انجام می شود. از این روش برای ساخت قطعات و فلزات نیمه ها در ساختارهای الکترونیکی استفاده می شود.
روش های سنتی و مدرن تولید ورق آلیاژی
روشهای سنتی و مدرن تولید ورق آلیاژی
تولید ورقهای آلیاژی در طول زمان دچار تحولات زیادی شده است. روشهای سنتی عمدتاً مبتنی بر عملیات دستی و تجهیزات مکانیکی ساده بودهاند، در حالی که روشهای مدرن از فناوریهای پیشرفته برای بهبود کیفیت، کاهش هزینهها و افزایش بهرهوری استفاده میکنند. در ادامه، روشهای سنتی و مدرن تولید ورقهای آلیاژی بررسی میشوند:
روشهای سنتی تولید ورق آلیاژی
1. چکشکاری و آهنگری (Forging & Hammering)
- در این روش، فلز مذاب ابتدا در قالبهایی ریخته شده و پس از سرد شدن، با استفاده از چکش یا پتکهای سنگین کوبیده و نازک میشود.
- بیشتر برای تولید ورقهای مسی، برنجی و فولادی به کار میرفت.
- معایب: عدم یکنواختی ضخامت، تنشهای داخلی زیاد، مصرف بالای انرژی و کارایی پایین.
2. نورد دستی (Manual Rolling)
- از غلتکهای دستی یا مکانیکی برای کاهش ضخامت ورقهای فلزی استفاده میشد.
- این روش برای تولید ورقهای نازک در حجم کم کاربرد داشت.
- معایب: دقت پایین، نیاز به نیروی انسانی زیاد و زمانبر بودن فرآیند.
3. ریختهگری سنتی (Traditional Casting)
- فلز مذاب در قالبهای ماسهای یا فلزی ریخته و سپس تحت عملیات حرارتی قرار میگرفت تا به ضخامت مورد نظر برسد.
- معایب: کیفیت سطحی پایین، احتمال وجود تخلخل و نیاز به ماشینکاری بعدی.
روشهای مدرن تولید ورق آلیاژی
1. نورد گرم (Hot Rolling)
- فلز مذاب ابتدا به شمش (تختال) تبدیل شده و سپس در دمای بالا از میان غلتکها عبور داده میشود.
- مزایا: کاهش تنشهای داخلی، بهبود استحکام، تولید در مقیاس انبوه.
- کاربرد: صنایع خودروسازی، کشتیسازی، پلسازی و لولههای فولادی.
2. نورد سرد (Cold Rolling)
- ورقهای تولید شده در نورد گرم، پس از خنک شدن تحت نورد سرد قرار میگیرند.
- مزایا: دقت ابعادی بالا، بهبود کیفیت سطحی، افزایش سختی.
- کاربرد: صنایع هوافضا، خودروسازی، تولید قطعات دقیق.
3. ریختهگری مداوم (Continuous Casting)
- در این روش، فلز مذاب مستقیماً به صورت ورقهای نازک ریختهگری میشود.
- مزایا: کاهش هزینه تولید، بهرهوری بالا، کاهش اتلاف مواد.
- کاربرد: تولید ورقهای فولادی و آلیاژهای خاص.
4. متالورژی پودر (Powder Metallurgy)
- پودر فلزی فشرده شده و در دمای بالا تفجوشی (Sintering) میشود.
- مزایا: امکان تولید آلیاژهای خاص، کنترل دقیق ترکیب شیمیایی.
- کاربرد: صنایع الکترونیک، هوافضا، مهندسی پزشکی.
5. روش نورد فوق نازک (Ultra-Thin Rolling)
- برای تولید ورقهای بسیار نازک مانند فویلهای آلومینیوم و فولاد ضدزنگ.
- مزایا: کاهش مصرف مواد، کیفیت سطحی بالا.
- کاربرد: صنایع بستهبندی، الکترونیک، پزشکی.
6. تکنولوژیهای نوین مانند چاپ سهبعدی فلزات (3D Metal Printing)
- از پودر فلزی و لیزر برای تولید ورقهای آلیاژی با شکلهای پیچیده استفاده میشود.
- مزایا: امکان تولید سفارشی، کاهش ضایعات مواد.
- کاربرد: صنایع پیشرفته مانند هوافضا و پزشکی.
مقایسه روشهای سنتی و مدرن
ویژگی |
روشهای سنتی |
روشهای مدرن |
دقت ابعادی |
کم |
بالا |
سرعت تولید |
کند |
سریع |
مصرف انرژی |
بالا |
بهینه |
کیفیت سطحی |
پایین |
بسیار بالا |
امکان تولید انبوه |
محدود |
گسترده |
هزینه تولید |
زیاد |
بهینه |
نتیجهگیری
روشهای سنتی بیشتر برای تولید ورقهای فلزی در مقیاس کوچک و با فناوریهای ساده کاربرد داشتند، در حالی که روشهای مدرن با استفاده از فناوریهای پیشرفته مانند نورد مداوم، ریختهگری پیوسته و متالورژی پودر، تولید سریعتر، مقرونبهصرفهتر و با کیفیت بالاتر را امکانپذیر کردهاند.
ورق های آلیاژی فرایند تولید
فرآیند تولید ورقهای آلیاژی
ورقهای آلیاژی از ترکیب فلزات مختلف ساخته میشوند تا خواص مکانیکی و فیزیکی مورد نیاز برای کاربردهای صنعتی مختلف را فراهم کنند. فرآیند تولید این ورقها شامل چندین مرحله از آمادهسازی مواد اولیه تا نورد و عملیات تکمیلی است.
مراحل تولید ورقهای آلیاژی
1. آمادهسازی مواد اولیه
- انتخاب فلز پایه (مانند فولاد، آلومینیوم، مس، نیکل) و عناصر آلیاژی (مانند کروم، مولیبدن، منگنز و تیتانیوم).
- توزین و ترکیب مواد برای دستیابی به ترکیب شیمیایی موردنظر.
2. ذوب و تصفیه (Melting & Refining)
- مواد اولیه در کورههای قوس الکتریکی یا کورههای القایی ذوب میشوند.
- ناخالصیها با روشهایی مانند تزریق گاز آرگون و استفاده از فلاکسها حذف میشوند.
- ترکیب شیمیایی با آزمایشهای متوالی کنترل شده و اصلاح میشود.
3. ریختهگری (Casting)
- روش ریختهگری پیوسته (Continuous Casting):
- فلز مذاب درون قالبهای متحرک ریخته شده و به صورت اسلب یا تختال (Slab) جامد میشود.
- این روش برای تولید انبوه و بهبود یکنواختی ساختاری استفاده میشود.
- روش ریختهگری سنتی (Ingot Casting):
- فلز مذاب در قالبهای جداگانه ریخته و پس از سرد شدن، به شمش (Ingot) تبدیل میشود.
- شمشها برای نورد به دماهای بالا گرم میشوند.
4. نورد گرم (Hot Rolling)
- تختالها یا شمشها در دمای بالا (بیش از ۱۱۰۰ درجه سانتیگراد برای فولاد) از میان غلتکهای نورد عبور داده میشوند.
- کاهش ضخامت و افزایش طول در چندین مرحله انجام میشود.
- محصول نهایی این مرحله ورقهای ضخیمتر هستند که برای تولید ورقهای نازکتر باید به مراحل بعدی بروند.
5. نورد سرد (Cold Rolling)
- ورقهای حاصل از نورد گرم پس از اسیدشویی و حذف پوستههای سطحی، تحت نورد سرد قرار میگیرند.
- این مرحله باعث افزایش سختی، بهبود دقت ابعادی و سطح صیقلیتر میشود.
6. عملیات حرارتی (Heat Treatment)
- بسته به نوع آلیاژ، عملیات حرارتی مانند آنیلینگ (Annealing) برای بهبود شکلپذیری و کاهش تنشهای داخلی انجام میشود.
- برخی آلیاژها برای افزایش سختی تحت عملیات کوئنچ و تمپرینگ قرار میگیرند.
7. پرداخت و اصلاح نهایی (Finishing & Cutting)
- ورقهای تولیدشده ممکن است تحت فرآیندهایی مانند سنگزنی، پولیش، روکشدهی (گالوانیزه، آنودایزینگ) و برش قرار گیرند.
- ضخامت و ابعاد نهایی ورقها مطابق استانداردهای صنعتی تنظیم میشود.
8. بازرسی و کنترل کیفیت
- آزمایشهای مکانیکی (کشش، سختی، ضربه) و بررسیهای میکروسکوپی برای اطمینان از کیفیت انجام میشوند.
- در صورت تأیید، ورقها بستهبندی و به بازار عرضه میشوند.
نتیجهگیری
تولید ورقهای آلیاژی یک فرآیند پیچیده و چندمرحلهای است که با کنترل دقیق مواد اولیه، فرآیندهای نورد و عملیات حرارتی، ورقهایی با خواص مکانیکی بهینه را ارائه میدهد. بسته به نوع آلیاژ و کاربرد نهایی، روشهای مختلفی برای تولید و اصلاح این ورقها مورد استفاده قرار میگیرد.